Research Interests
- Tool Design and Manufacturing
- Additive Manufacturing for Rapid Prototyping, Tooling, and Manufacturing
- Polymer Processes including Micromoulding
- Processing of Engineering and High Performance Polymers
- Simulation of Polymer Processing
- Characterisation of Polymer Materials and Polymer Parts
- Composite Design, Manufacturing and Testing
Lead Investigator of Polymer Engineering Research and Innovation (PERI) Unit
The PERI Lab boasts state-of-the-art equipment for both conventional polymer processing and advanced polymer-based additive manufacturing (3D printing), as well as comprehensive polymer characterization and testing.
Funded Research Projects
- Active Vacuum Venting System for Non-Sealed Moulding (VENTO)
Funding Body: Xjenza Malta, GoToMarket: Accelerator Programme 2025
Role: Principal Investigator and Coordinator
- Eco-Friendly and Additively Manufacturable Thermoplastic Vulcanized Rubbers using Deep Eutectic Solvents (AMBER)
Funding: Xjenza Malta, Sino-Malta 2024 (June 2025 - June 2027)
Role: Principal Investigator and Coordinator
- High Yield Pellet Extrusion 3D Printing (HYP3D)
Funding: Xjenza Malta, Technology Extension Support Programme (TESP)(May 2025 - April 2027)
Role: Partner
- Elucidation of Crystallisation Process Using FFF 3D Printer Assisted IR Thermal Imaging Technique on Plastic Waste (CPW)
Funding Body: HORIZON TMA MSCA Postdoctoral Fellowships programme (May 2024 - April 2026)
Role: Supervisor
- Development of an Innovative Pellet 3D Printer (SPELL3D)
Funding Body: Malta Council for Science and Technology through the FUSION: R&I Technology Development Programme (R&I-2022-010-T)
Role: Principal Investigator and Coordinator
- Developing a Go-To-Market Strategy for an Innovative MALTI3D Printing System (GO2MALTI3D)
Funding Body: Malta Council for Science and Technology through the FUSION R&I Go To Market: Accelerator Programme (R&I-2018-009-A)
Role: Principal Investigator and Coordinator
- Concrete Reinforced with 3D Printed Recycled PET Structure (CoRePET)
Funding: MCST Technology Extension Support Programme (TESP)(2023)
Role: Partner
- Rheometric 3D Printing (REO3D)
Funding Body: Malta Council for Science and Technology through Research Excellence Programme (REP) (2023)
Role: Principal Investigator and Coordinator
- Green Laser Post-Processing in Additive Manufacturing (GLAM)
Funding: MCST Sino-Malta 2022
Role: Partner
- Combining 3D printing and Microinjection moulding for the fabrication of polymer components with embedded miniature hollow cavities (MICORE)
Funding Body: Malta Council for Science and Technology through Research Excellence Programme (REP) (2022)
Role: Partner and Work Package Leader of Experimental Investigation and Performance Evaluation of the 3DP + MIM Process Chain
- Development and Performance Analysis of Sustainable Conformal Cooling Channels (CONFORM)
Funding Body: University of Malta, Transdisciplinary Research and Knowledge Exchange Complex (TRAKE) Postdoc (2022)
Role: Principal Investigator and Coordinator
- Innovative Mold Vacuum System (VacuUM)
Funding Body: Malta Council for Science and Technology through the FUSION: R&I Technology Development Programme (R&I-2020-004T)
Role: Principal Investigator and Coordinator
- Inflatable Arthroscopic Device as an Alternative to Knee Replacement Surgery (MALTAKNEE)
Funding Body: Malta Council for Science and Technology through the FUSION: R&I Technology Development Programme (R&I-2019-027-T),
Role: Partner and Leader of work package Device Design and Casting
- Innovative Multi-Axis and Multi-Head 3D Printer (MALTI3D)
Funding Body: Malta Council for Science and Technology through the FUSION: R&I Technology Development Programme (R&I-2018-009T)
Role: Principal Investigator and Coordinator
- Biodegradable Iron for Orthopaedic Scaffold Applications (BioSA)
- Funding Body: Malta Council for Science and Technology through the FUSION: R&I Technology Development Programme - (R&I-2017-037T)
Role: Partner and Leader of a work package
- Development of 3D Printing Head with Laser Melting for Printers Using Fused Filament Fabrication (FFF) Technology (LASeeeR)
Funding Body: Malta Council for Science and Technology through the FUSION: R&I Technology Development Programme - (R&I-2017-025T)
Role: Partner and Leader of work packages Filament Development and Printing Head Holder Development
- Exploiting Multi-Material Micro Injection Moulding for Enhancing Manufacturing Competitiveness (EX-MMIM)
Funding Body: Malta Council for Science and Technology through the R&I Programme (R&I 2012-002)
Role: Key Expert 1
Website: www.exmmim.com
Back to Top ^
Examples for Research Results
Rapid Tooling Using Electron Beam Melting
Borg A.K. and Rochman A., Design and Manufacture of Injection Mold Inserts Using Electron Beam Melting, Journal of Manufacturing Science and Engineering, in Special Issue: Additive Manufacturing (AM) and 3 D Printing, December 2014, Vol. 136, p. 061011
The capability of producing injection tool inserts using an additive manufacturing (AM) technology was investigated. Using electron beam melting (EBM), the restriction of drilling straight cooling channels could be eliminated and freeform channels with sufficient powder removal were achieved. EBM parameters and the design of the cooling channels strongly influence the sintering degree of the powder trapped in the channels and thus the ease of the powder removal. Despite the low heat conductivity of the new inserts made from Ti6Al4V, the cooling performance was the same as for the conventional inserts. However, the use of Ti6Al4V is advantageous since the expanding agent used in injection molding is very corrosive.
Back to Top ^
An Investigation of Influences of Melt Mixer on Injection Moulding Process and Part Quality of Thermoset Elastomers
M.Sc. by Research, Keith Zahra, 2015
Zahra K. and Rochman A.,Polymer Engineering and Science, vol. 58(4), 2017, pp. 521-527
In this study, various static melt mixers inside the nozzle chamber, together forming a mixing nozzle, were developed. Their performance in injection molding process was investigated using three thermoset elastomer materials with significantly different viscosity, namely nitrile butadiene rubber (NBR), ethylene propylenediene monomer (EPDM) and fluorocarbon (FKM). The aim of this study was to minimize one of the drawbacks in injection molding resulted from the relatively short plasticizing screw. Using a short plasticizing screw, polymers having high concentrations of additives, such as thermoset elastomers, might not mix homogeneously within the short time period during the plasticizing stage. The use of these melt mixers resulted in better homogeneity and properties of the molded parts despite a curing time reduction of 10 s. This was due to the increase in mixing and shearing introduced a higher rate of crosslinking formation in the molded parts.
Back to Top ^
Combining Additive and Subtractive Manufacturing
M.Sc. By Research, Christian Spiteri, 2013
Electron Beam Melting (EBM) is an Additive Manufacturing (AM) technique that builds parts layer by layer and thus permits high geometry flexibility and short lead times. However, this system has its own limitations. EBM is considered to deliver near-net shape parts owing to their rough surface finish and its limited control on dimensional accuracy. Surrounding powder during the building process gets sintered to the parts’ surfaces which have pronounced mountain valley topography. These considerations justify the process chain proposed in this project. Subtractive Electric Discharge Machining (EDM) was chosen as a finishing process to post-process parts produced with EBM. Its ability to process complex shapes in difficult to machine materials, such as Titanium alloys, makes it the ideal choice to combine with EBM.
The first set of experiments analysed the metallographic effect of EDM on the surface of Ti6Al4V-ELI parts manufactured by the EBM process. The surface produced after finishing had a much improved topography without the original surface deficiencies. The surface roughness of the finished products could also be varied according to the parameters used. The bulk microstructure consisted of the typical fine α and β phases while a recast layer and a heat affected zone were both created at the surface after finishing. The thickness of the recast layer decreases with lower machine roughness settings due to lower discharge energy. Additionally, EDM with Kerosene dielectric fluid and Copper electrodes increased the Carbon and Copper content in the surface of the parts. The second phase of the project investigated the surface quality and the dimensional accuracy capabilities obtained with the proposed process chain.
Back to Top ^
Integrative Development of Injection Moulded Fibre-Reinforced Polymer Parts for Highly Loaded Applications
M.Sc. By Research, Timo Dolde, 2012
Using a highly-loaded pocket wheel as a case study, the aim of the work was to analyse the whole development process, to show the main problems and to find solution how they can be solved with currently available tools and methods. In this work, currently available simulation methods for fibre reinforced parts like injection moulding simulation, process-structure-linking, FEM stress calculation, multi-scale-modeling and topology optimisation were used.
The development process is described from conception phase in the beginning, over CAD-modeling, FEM calculation and optimisation, filling study and the mold design till the mechanical testing of prototypes in the end.
The result of the project was an innovative pocket wheel made from PA66+PA6I/X with 50% glass fibre, with a calculated lifetime of 1.6 105 load cycles at a load of 550 kg. One of the most important perceptions is that the shrinkage in such a part can be highly anisotropic (ratio 10:1) and the percentage shrinkage is much higher than for thin-walled parts. Without this knowledge, a time and cost consuming reversion of the mould is necessary.
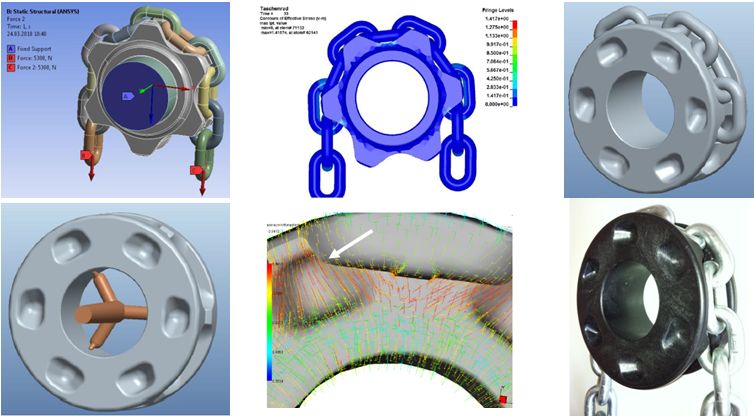
Back to Top ^